Improving training in Manufacturing
– through interactive 3D visualisations and automation
What our customers say
Virtual training has many advantages. It is quicker, cheaper and more flexible than learning with reproduced hardware prototypes. An initial evaluation of VISTRA revealed that people trained on the virtual system make less mistakes (down 40 percent) than people trained solely on prototypes.
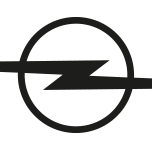
Frank Arlt
Opel
The collaboration with Sentio Simulations has been great and the solution was delivered on time in a few months. We think this innovative technology has a lot of potential and that the business case for virtual operator training is very interesting.
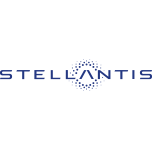
Fernando Caamano, General Assembly, Engineering Manager
Stellantis
VISTRA is a really good and helpful program to support the training, in parallel to the physical training.
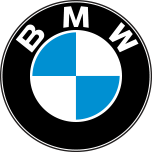
Oliver Meissner, Training Manager
BMW
We think this innovative technology has a lot of potential and that the business case for virtual operator training is very interesting.
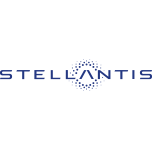
Fernando Caamano, General Assembly, Engineering Manager
Stellantis
Faster and better training
Vistra automatically generates interactive virtual learning content in 3D.
The training interface is built on the latest research on digital learning. It means that operators learn the procedures faster and that the learning sticks.
Say goodbye to manual work on training content
The simulations Vistra generates come from the customers’ existing engineering data. That means Training Managers no longer need to spend endless hours manually creating and updating learning content.
Less rework and wastage
Sentio has documented again and again that Vistra training means fewer mistakes and less calls for help on the assembly line. This means less rework and parts wastage – two significant costs for most assembly plants.
Scale your training limitlessly
The Vistra software architecture has been designed for companies with hundreds of thousands of employees and it has been battle-tested in many different settings and countries. Its unique integration module makes automation easy and scaling to many plants effortless.
Use cases
Examples for interactive virtual operator training
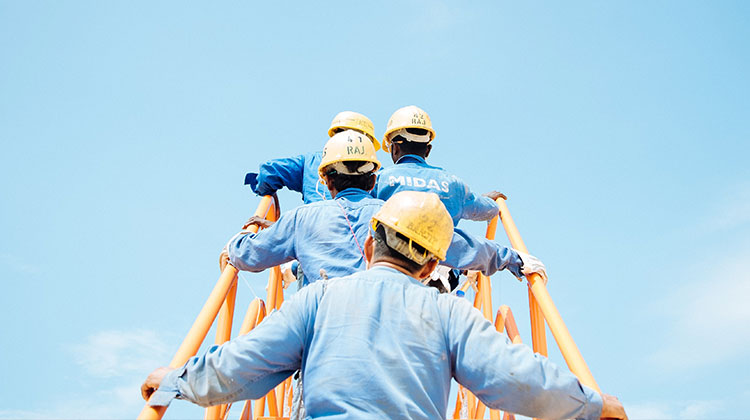
Ramp-up or high employee turnover
Plants that are starting new production has a special need for training. The same can be said of plants with a generally high employee turnover – e.g. plants with many employees on short term contracts. These plants will have an exceptionally strong ROI when choosing Vistra.
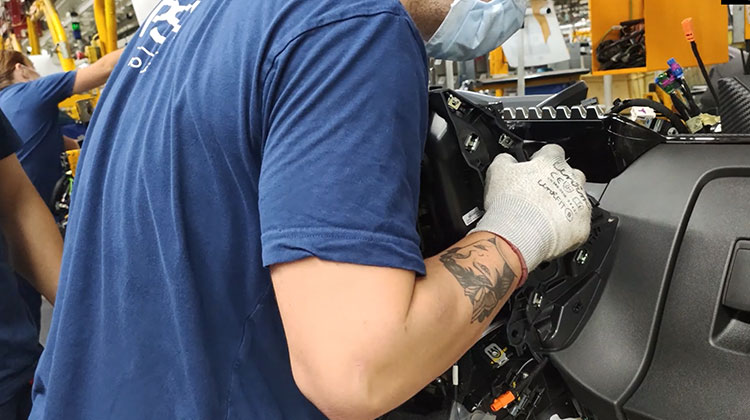
Get quality improvements in Assembly
Many plants are struggling with minor quality issues like paint scratches or parts that break from inaccurate handling. These issues can be very costly when you factor in all the costs in time and parts. Vistra can help clean up these defects and that represents a strong business case.
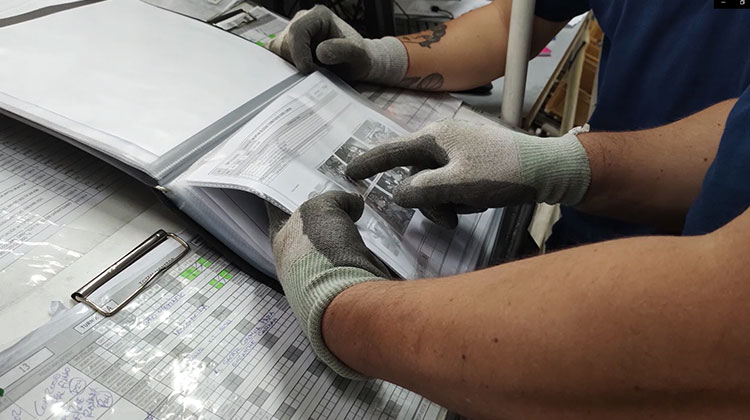
Handle your changes more effiently
Many attempts to digitalize training in Manufacturing has failed because the learning content grows out-of-date when line balancing, or other changes to tools, parts or processes mean that the training is no longer accurate. Not with Vistra! It always gets its data from the most recent source.